Materials and Properties
Intricate 3D components are produced from thermo, light-curing plastics (photopolymers) in the stereolithography (SLA) 3D printing process. In thin layers (“slices”), the plastic is cured from a liquid bath by a UV laser and, little by little, built up into a three-dimensional object. For the stereolithography process, various plastic compounds made of epoxy, vinyl or acrylic resins are processed in layers with thicknesses from 0.016 mm (16 microns).
Get more information about the method and technology.
These plastics are used for stereolithography
Epoxy resins are the most commonly used material group in stereolithography. This synthetic resin with good electrical-insulation properties and high heat-resistance is also known as reaction resin. Thanks to its outstanding product properties, such as variable flexibility, low impact sensitivity and the high dimensional accuracy of the end products, the photopolymer is suitable for the production of complex, detailed prototypes that can hold up to initial functional tests.
Epoxy Resins with Various Material Properties
An extensive range of epoxy resins with a wide range of material properties is available on the market: The durable VisiJet SL Tough, for instance, has a material behavior similar to that of the ABS used by FDM printers and is characterized by its high impact-resistance and reproduction accuracy. The VisiJet SL Clear synthetic resin from the same product line is used to produce transparent objects with high clarity. The resistant VisiJet SL HiTemp is suitable for the use in high temperatures which, with its thermal stability up to 130°C, is used for testing components in the engine compartment, among other things.
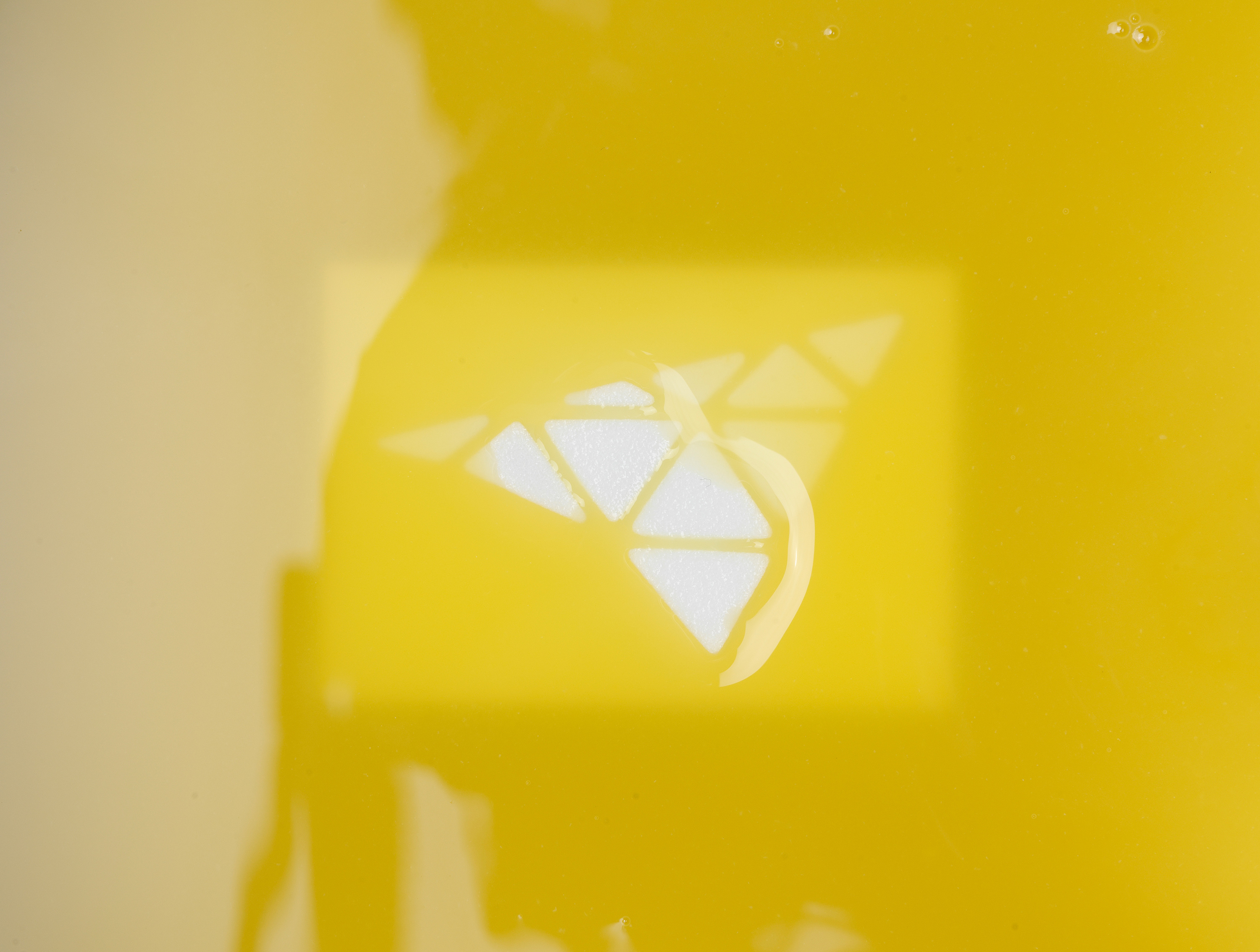